Porosität, hohlraumartige Diskontinuitäten, die durch Gaseinschlüsse während der Erstarrung entstehen, ist ein häufiger, aber lästiger Defekt beim MIG-Schweißen, der mehrere Ursachen haben kann.Es kann in halbautomatischen oder robotergestützten Anwendungen auftreten und erfordert in beiden Fällen die Entfernung und Nacharbeit – was zu Ausfallzeiten und höheren Kosten führt.
Die Hauptursache für Porosität beim Stahlschweißen ist Stickstoff (N2), der sich im Schweißbad einlagert.Wenn das Flüssigkeitsbad abkühlt, verringert sich die Löslichkeit von N2 deutlich und N2 tritt aus der Stahlschmelze aus und bildet Blasen (Poren).Beim verzinkten/Galvanneal-Schweißen kann verdampftes Zink in das Schweißbad eingerührt werden, und wenn nicht genügend Zeit zum Entweichen bleibt, bevor das Bad erstarrt, bildet es Porosität.Beim Aluminiumschweißen wird die gesamte Porosität durch Wasserstoff (H2) verursacht, genauso wie N2 bei Stahl wirkt.
Schweißporosität kann äußerlich oder innerlich auftreten (oft als Porosität unter der Oberfläche bezeichnet).Es kann sich auch an einem einzelnen Punkt der Schweißnaht oder über die gesamte Länge entwickeln, was zu schwachen Schweißnähten führt.
Wenn Sie wissen, wie Sie einige Hauptursachen für Porosität identifizieren und diese schnell beheben können, können Sie Qualität, Produktivität und das Endergebnis verbessern.
Schlechte Schutzgasabdeckung
Eine schlechte Schutzgasabdeckung ist die häufigste Ursache für Schweißporosität, da dadurch atmosphärische Gase (N2 und H2) das Schweißbad verunreinigen können.Eine unzureichende Abdeckung kann aus mehreren Gründen auftreten, unter anderem aufgrund einer schlechten Schutzgasdurchflussrate, Undichtigkeiten im Gaskanal oder zu viel Luftstrom in der Schweißzelle.Auch zu hohe Reisegeschwindigkeiten können ein Grund sein.
Wenn ein Bediener vermutet, dass ein schlechter Durchfluss das Problem verursacht, versuchen Sie, den Gasdurchflussmesser anzupassen, um sicherzustellen, dass die Rate ausreichend ist.Bei Verwendung eines Sprühübertragungsmodus sollte beispielsweise ein Durchfluss von 35 bis 50 Kubikfuß pro Stunde (cfh) ausreichen.Das Schweißen bei höheren Stromstärken erfordert eine Erhöhung der Durchflussrate, es ist jedoch wichtig, die Rate nicht zu hoch einzustellen.Dies kann bei einigen Pistolenkonstruktionen zu Turbulenzen führen, die die Schutzgasabdeckung beeinträchtigen.
Es ist wichtig zu beachten, dass unterschiedlich konstruierte Pistolen unterschiedliche Gasflusseigenschaften haben (siehe zwei Beispiele unten).Der „Sweet Spot“ der Gasdurchflussrate ist bei der oberen Ausführung viel größer als bei der unteren Ausführung.Dies ist etwas, was ein Schweißingenieur beim Einrichten der Schweißzelle berücksichtigen muss.
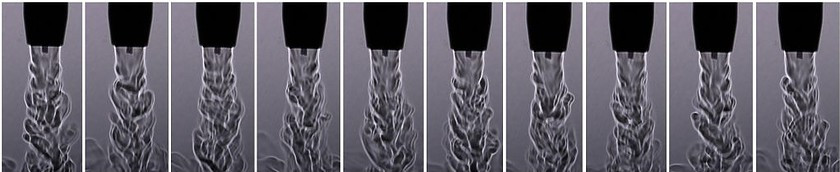
Design 1 zeigt einen gleichmäßigen Gasfluss am Düsenaustritt
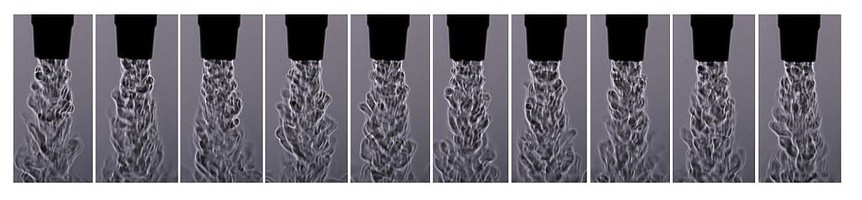
Design 2 zeigt turbulente Gasströmung am Düsenaustritt.
Überprüfen Sie außerdem den Gasschlauch, die Armaturen und Anschlüsse sowie die O-Ringe am Stromanschluss der MIG-Schweißpistole auf Beschädigungen.Bei Bedarf ersetzen.
Wenn Sie Ventilatoren zum Kühlen von Bedienern oder Teilen in einer Schweißzelle verwenden, achten Sie darauf, dass diese nicht direkt auf den Schweißbereich gerichtet sind, wo sie die Gasabdeckung stören könnten.Platzieren Sie ein Sieb in der Schweißzelle, um es vor externer Luftströmung zu schützen.
Berühren Sie das Programm bei Roboteranwendungen erneut, um sicherzustellen, dass ein ordnungsgemäßer Abstand zwischen Spitze und Werkstück vorhanden ist, der je nach gewünschter Länge des Lichtbogens typischerweise ½ bis 3/4 Zoll beträgt.
Verringern Sie schließlich die Fahrgeschwindigkeit, wenn die Porosität weiterhin besteht, oder wenden Sie sich an einen MIG-Brennerlieferanten für andere Frontend-Komponenten mit besserer Gasabdeckung
Grundmetallverunreinigung
Eine weitere Ursache für Porosität ist die Verunreinigung durch unedle Metalle – von Öl und Fett bis hin zu Walzzunder und Rost.Auch Feuchtigkeit kann diese Diskontinuität begünstigen, insbesondere beim Aluminiumschweißen.Diese Arten von Verunreinigungen führen typischerweise zu äußerer Porosität, die für den Bediener sichtbar ist.Verzinkter Stahl ist anfälliger für Porosität unter der Oberfläche.
Um äußere Porosität zu verhindern, reinigen Sie das Grundmaterial vor dem Schweißen gründlich und erwägen Sie die Verwendung eines Schweißdrahtes mit Metallkern.Diese Art von Draht weist einen höheren Gehalt an Desoxidationsmitteln auf als Massivdraht und ist daher toleranter gegenüber verbleibenden Verunreinigungen auf dem Grundmaterial.Lagern Sie diese und alle anderen Drähte immer an einem trockenen, sauberen Ort mit einer ähnlichen oder etwas höheren Temperatur als die Pflanze.Dadurch wird die Kondensation minimiert, die Feuchtigkeit in das Schweißbad einbringen und Porosität verursachen könnte.Lagern Sie Kabel nicht in einem Kühlhaus oder im Freien.
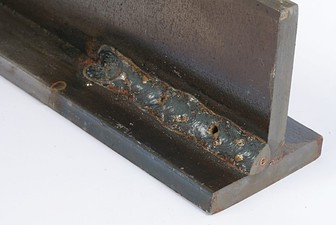
Porosität, hohlraumartige Diskontinuitäten, die durch Gaseinschlüsse während der Erstarrung entstehen, ist ein häufiger, aber lästiger Defekt beim MIG-Schweißen, der mehrere Ursachen haben kann.
Beim Schweißen von verzinktem Stahl verdampft das Zink bei einer niedrigeren Temperatur als der Stahl schmilzt, und hohe Fahrgeschwindigkeiten führen tendenziell dazu, dass das Schweißbad schnell gefriert.Dadurch kann Zinkdampf im Stahl eingeschlossen werden, was zu Porosität führt.Bekämpfen Sie diese Situation, indem Sie die Fahrgeschwindigkeiten überwachen.Erwägen Sie auch hier einen speziell entwickelten Metalldraht (Flussmittelformel), der das Entweichen von Zinkdampf aus dem Schweißbad fördert.
Verstopfte und/oder zu kleine Düsen
Auch verstopfte und/oder zu kleine Düsen können zu Porosität führen.In der Düse und auf der Oberfläche der Kontaktspitze und des Diffusors können sich Schweißspritzer ansammeln, die zu einer eingeschränkten oder turbulenten Schutzgasströmung führen.Beide Situationen führen dazu, dass das Schweißbad nur unzureichend geschützt ist.
Erschwerend kommt hinzu, dass die Düse für die Anwendung zu klein ist und anfälliger für eine stärkere und schnellere Bildung von Spritzern ist.Kleinere Düsen können einen besseren Verbindungszugang ermöglichen, behindern jedoch aufgrund der kleineren Querschnittsfläche für den Gasfluss auch den Gasfluss.Berücksichtigen Sie immer die Variable zwischen Kontaktspitze und Düsenüberstand (oder -aussparung), da dies ein weiterer Faktor sein kann, der den Schutzgasfluss und die Porosität bei Ihrer Düsenauswahl beeinflusst.
Stellen Sie daher sicher, dass die Düse groß genug für die Anwendung ist.Typischerweise erfordern Anwendungen mit hohem Schweißstrom und größeren Drahtstärken eine Düse mit größeren Bohrungsgrößen.
Überprüfen Sie bei halbautomatischen Schweißanwendungen regelmäßig, ob Schweißspritzer in der Düse vorhanden sind, und entfernen Sie diese mit einer Schweißzange (Schweißgerät) oder tauschen Sie die Düse bei Bedarf aus.Stellen Sie bei dieser Inspektion sicher, dass die Kontaktspitze in gutem Zustand ist und der Gasdiffusor über freie Gasanschlüsse verfügt.Bediener können auch Anti-Spritzer-Mittel verwenden, müssen jedoch darauf achten, die Düse nicht zu weit oder zu lange in das Mittel einzutauchen, da zu große Mengen des Mittels das Schutzgas verunreinigen und die Düsenisolierung beschädigen können.
Investieren Sie bei einem Roboterschweißvorgang in eine Düsenreinigungsstation oder eine Reibahle, um die Bildung von Spritzern zu verhindern.Dieses Peripheriegerät reinigt die Düse und den Diffusor während routinemäßiger Produktionspausen, sodass die Zykluszeit dadurch nicht beeinträchtigt wird.Düsenreinigungsstationen sollen in Verbindung mit einem Anti-Spritzer-Sprühgerät funktionieren, das eine dünne Schicht der Verbindung auf die vorderen Komponenten aufträgt.Zu viel oder zu wenig Anti-Spritzer-Flüssigkeit kann zu zusätzlicher Porosität führen.Die Hinzufügung eines Luftstrahls zu einem Düsenreinigungsprozess kann auch dazu beitragen, lose Spritzer von den Verbrauchsmaterialien zu entfernen.
Aufrechterhaltung von Qualität und Produktivität
Durch die sorgfältige Überwachung des Schweißprozesses und die Kenntnis der Ursachen der Porosität lassen sich relativ einfach Lösungen umsetzen.Dies kann dazu beitragen, eine längere Lichtbogen-Einschaltzeit, qualitativ hochwertige Ergebnisse und mehr gute Teile durch die Produktion zu gewährleisten.
Zeitpunkt der Veröffentlichung: 02.02.2020