Mit Präzision wird die Feinheit des Werkstückprodukts angegeben. Es ist ein spezieller Begriff zur Bewertung der geometrischen Parameter der Bearbeitungsoberfläche und ein wichtiger Indikator zur Messung der Leistung von CNC-Bearbeitungszentren. Im Allgemeinen wird die Bearbeitungsgenauigkeit anhand des Toleranzgrades gemessen. Je niedriger die Note, desto höher die Genauigkeit. Drehen, Fräsen, Hobeln, Schleifen, Bohren und Bohren sind gängige Bearbeitungsformen von CNC-Bearbeitungszentren. Welche Bearbeitungsgenauigkeit sollen diese Bearbeitungsverfahren also erreichen?
1.Drehgenauigkeit
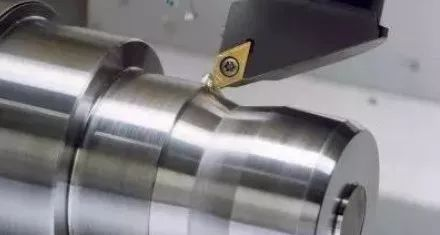
Unter Drehen versteht man den Schneidvorgang, bei dem sich das Werkstück dreht und sich das Drehwerkzeug in einer geraden Linie oder Kurve in der Ebene bewegt, wodurch die inneren und äußeren zylindrischen Flächen, Endflächen, konischen Flächen, Formflächen und Gewinde bearbeitet werden Werkstück.
Die Oberflächenrauheit beim Drehen beträgt 1,6–0,8 μm.
Beim Schruppdrehen sind eine große Schnitttiefe und eine große Vorschubgeschwindigkeit erforderlich, um die Dreheffizienz zu verbessern, ohne die Schnittgeschwindigkeit zu verringern, und die Anforderung an die Oberflächenrauheit beträgt 20–10 µm.
Xinfa CNC-Werkzeuge zeichnen sich durch gute Qualität und niedrigen Preis aus. Weitere Informationen finden Sie unter:CNC-Werkzeughersteller - China CNC-Werkzeugfabrik und Lieferanten (xinfatools.com)
Beim Vorschlichten und Schlichtdrehen werden hohe Geschwindigkeiten, kleine Vorschübe und Schnitttiefen verwendet. Die Oberflächenrauheit beträgt 10–0,16 µm.
Das fein polierte Diamantdrehwerkzeug der Hochpräzisionsdrehmaschine kann Nichteisenmetallwerkstücke mit hoher Geschwindigkeit und einer Oberflächenrauheit von 0,04–0,01 um drehen. Diese Art des Drehens wird auch „Spiegeldrehen“ genannt.
2. Fräsen Unter Präzisionsfräsen versteht man den Einsatz rotierender Mehrschneidewerkzeuge zum Schneiden von Werkstücken, was eine hocheffiziente Bearbeitungsmethode darstellt.
Geeignet für die Bearbeitung von Ebenen, Nuten und verschiedenen Keilverzahnungen, Zahnrädern, Gewindeformen und anderen Sonderflächen.
Die Oberflächenrauheit beim Fräsen beträgt im Allgemeinen 6,3–1,6 μm. Die Oberflächenrauheit beim Grobfräsen beträgt 5–20 μm.
Die Oberflächenrauheit beim Vorschlichtfräsen beträgt 2,5–10 μm. Die Oberflächenrauheit beim Feinfräsen beträgt 0,63–5 μm.
3. Hobelgenauigkeit
Hobeln ist eine Schneidmethode, bei der mit einem Hobel eine horizontale, relative, lineare Hin- und Herbewegung auf dem Werkstück ausgeführt wird, die hauptsächlich für die Formbearbeitung von Teilen verwendet wird. Die Oberflächenrauheit beim Hobeln beträgt Ra6,3-1,6μm.
Die Oberflächenrauheit beim Grobhobeln beträgt 25–12,5 μm. Die Oberflächenrauheit beim Halbschlichthobeln beträgt 6,2–3,2 μm. Die Oberflächenrauheit beim Feinhobeln beträgt 3,2–1,6 μm.
4. Schleifgenauigkeit Unter Schleifen versteht man die Bearbeitungsmethode, bei der mit Schleifmitteln und Schleifwerkzeugen überschüssiges Material vom Werkstück abgetrennt wird. Es gehört zur Feinverarbeitung und wird häufig im Maschinenbau eingesetzt.
Schleifen wird normalerweise zum Halbschlichten und Schlichten verwendet, und die Oberflächenrauheit beträgt im Allgemeinen 1,25–0,16 μm.
Die Oberflächenrauheit beim Präzisionsschleifen beträgt 0,16–0,04 μm.
Die Oberflächenrauheit beim Ultrapräzisionsschleifen beträgt 0,04–0,01 μm. Die Oberflächenrauheit beim Spiegelschleifen kann weniger als 0,01 μm erreichen.
5. Langweilig
Es handelt sich um einen Schneidprozess, bei dem ein Werkzeug verwendet wird, um den Innendurchmesser eines Lochs oder einer anderen kreisförmigen Kontur zu vergrößern. Der Anwendungsbereich reicht im Allgemeinen vom Halbschruppen bis zum Schlichten. Das verwendete Werkzeug ist in der Regel ein einschneidiges Bohrwerkzeug (Bohrstange genannt).
Die Bohrgenauigkeit von Stahlwerkstoffen kann im Allgemeinen 2,5–0,16 μm erreichen.
Die Bearbeitungsgenauigkeit beim Präzisionsbohren kann 0,63–0,08 μm erreichen.
Zeitpunkt der Veröffentlichung: 03.09.2024