Das MIG-Schweißen erfordert wie jedes andere Verfahren Übung, um Ihre Fähigkeiten zu verfeinern. Für Neueinsteiger kann der Aufbau einiger Grundkenntnisse Ihren MIG-Schweißvorgang auf die nächste Stufe heben. Oder wenn Sie schon eine Weile schweißen, kann eine Auffrischung nie schaden. Betrachten Sie diese häufig gestellten Fragen und die dazugehörigen Antworten als Schweißtipps, die Ihnen als Orientierungshilfe dienen.
1. Welche Antriebsrolle soll ich verwenden und wie stelle ich die Spannung ein?
Die Größe und Art des Schweißdrahtes bestimmt die Antriebsrolle, um eine gleichmäßige und gleichmäßige Drahtförderung zu gewährleisten. Es gibt drei gängige Optionen: V-gerändelt, U-Nut und V-Nut.
Kombinieren Sie gas- oder selbstgeschützte Drähte mit V-gerändelten Antriebsrollen. Diese Schweißdrähte sind aufgrund ihrer röhrenförmigen Bauweise weich; Die Zähne der Antriebsrollen greifen den Draht und schieben ihn durch den Vorschubantrieb. Verwenden Sie U-Nut-Antriebsrollen zum Zuführen von Aluminium-Schweißdraht. Die Form dieser Antriebsrollen verhindert eine Beschädigung dieses weichen Drahtes. Antriebsrollen mit V-Nut sind die beste Wahl für Massivdraht.
Um die Spannung der Antriebsrollen einzustellen, lösen Sie zunächst die Antriebsrollen. Erhöhen Sie langsam die Spannung, während Sie den Draht in Ihre behandschuhte Hand führen. Fahren Sie fort, bis die Spannung eine halbe Umdrehung über dem Drahtschlupf liegt. Halten Sie die Pistole während des Vorgangs so gerade wie möglich, um ein Knicken des Kabels zu vermeiden, was zu einer schlechten Drahtzufuhr führen könnte.

Das Befolgen einiger wichtiger Best Practices in Bezug auf Schweißdraht, Antriebsrollen und Schutzgas kann dazu beitragen, gute Ergebnisse beim MIG-Schweißprozess sicherzustellen.
2. Wie erziele ich mit meinem MIG-Schweißdraht die besten Ergebnisse?
MIG-Schweißdrähte unterscheiden sich in ihren Eigenschaften und Schweißparametern. Überprüfen Sie immer die Spezifikation oder das Datenblatt des Drahts, um festzustellen, welche Stromstärke, Spannung und Drahtvorschubgeschwindigkeit der Hersteller des Zusatzwerkstoffs empfiehlt. Datenblätter werden in der Regel mit dem Schweißdraht geliefert oder können von der Website des Zusatzwerkstoffherstellers heruntergeladen werden. Diese Blätter enthalten auch Schutzgasanforderungen sowie Kontakt-zu-Werkstück-Abstand (CTWD) und Empfehlungen zur Schweißdrahtverlängerung oder zum Überstehen des Schweißdrahts.
Stickout ist besonders wichtig, um optimale Ergebnisse zu erzielen. Ein zu langer Stickout führt zu einer kälteren Schweißnaht, verringert die Stromstärke und verringert die Verbindungsdurchdringung. Ein kürzerer Stickout sorgt normalerweise für einen stabileren Lichtbogen und eine bessere Niederspannungsdurchdringung. Als Faustregel gilt, dass die beste Stickout-Länge die kürzeste für die Anwendung zulässige Länge ist.
Auch die ordnungsgemäße Lagerung und Handhabung des Schweißdrahtes ist für gute MIG-Schweißergebnisse von entscheidender Bedeutung. Bewahren Sie die Spule an einem trockenen Ort auf, da Feuchtigkeit den Draht beschädigen und möglicherweise zu durch Wasserstoff verursachten Rissen führen kann. Tragen Sie beim Umgang mit dem Kabel Handschuhe, um es vor Feuchtigkeit oder Schmutz durch Ihre Hände zu schützen. Wenn sich der Draht im Drahtvorschubgerät befindet, aber nicht verwendet wird, decken Sie die Spule ab oder entfernen Sie sie und legen Sie sie in eine saubere Plastiktüte.
3. Welche Kontaktmulde soll ich verwenden?
Die Aussparung der Kontaktspitze bzw. die Position der Kontaktspitze innerhalb der MIG-Schweißdüse hängt vom Schweißmodus, dem Schweißdraht, der Anwendung und dem verwendeten Schutzgas ab. Im Allgemeinen sollte mit zunehmendem Strom auch die Aussparung der Kontaktspitze größer werden. Hier sind einige Empfehlungen.
Eine 1/8- oder 1/4-Zoll-Aussparung eignet sich gut zum Schweißen mit mehr als 200 Ampere beim Sprüh- oder Hochstrom-Impulsschweißen, wenn ein Metallkerndraht und argonreiche Schutzgase verwendet werden. In diesen Fällen können Sie einen Kabelüberstand von 1/2 bis 3/4 Zoll verwenden.
Halten Sie Ihre Kontaktspitze bündig mit der Düse, wenn Sie im Kurzschluss- oder Schwachstrom-Impulsmodus mit weniger als 200 Ampere schweißen. Es wird ein Drahtüberstand von 1/4 bis 1/2 Zoll empfohlen. Mit einem 1/4-Zoll-Überstand im Kurzschlussbereich können Sie insbesondere dünnere Materialien schweißen, ohne dass das Risiko eines Durchbrennens oder einer Verformung besteht.
Beim Schweißen schwer zugänglicher Verbindungen und bei weniger als 200 Ampere können Sie die Kontaktspitze 1/8 Zoll aus der Düse herausziehen und einen 1/4 Zoll Stickout verwenden. Diese Konfiguration ermöglicht einen besseren Zugang zu schwer zugänglichen Verbindungen und eignet sich gut für Kurzschluss- oder Niedrigstrom-Impulsmodi.
Denken Sie daran, dass die richtige Aussparung der Schlüssel zur Reduzierung der Möglichkeit von Porosität, unzureichender Eindringung und Durchbrennung sowie zur Minimierung von Spritzern ist.
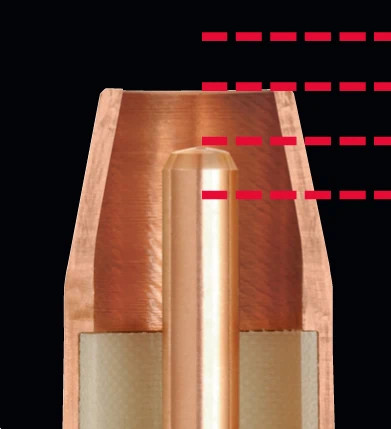
Die ideale Position der Kontaktspitzenvertiefung variiert je nach Anwendung. Als Faustregel gilt: Mit steigendem Strom sollte auch die Aussparung größer werden.
4. Welches Schutzgas eignet sich am besten für meinen MIG-Schweißdraht?
Welches Schutzgas Sie wählen, hängt vom Draht und der Anwendung ab. CO2 sorgt für eine gute Durchdringung beim Schweißen dickerer Materialien und Sie können es bei dünneren Materialien verwenden, da es dazu neigt, kühler zu werden, was die Gefahr eines Durchbrennens verringert. Für noch mehr Schweißdurchdringung und hohe Produktivität verwenden Sie eine Gasmischung aus 75 Prozent Argon und 25 Prozent CO2. Diese Kombination erzeugt auch weniger Spritzer als CO2, sodass nach dem Schweißen weniger Nacharbeiten erforderlich sind.
Verwenden Sie ein Schutzgas aus 100 Prozent CO2 oder eine Mischung aus 75 Prozent CO2 und 25 Prozent Argon in Kombination mit einem Massivdraht aus Kohlenstoffstahl. Aluminiumschweißdraht erfordert Argon als Schutzgas, während Edelstahldraht am besten mit einer Dreifachmischung aus Helium, Argon und CO2 funktioniert. Empfehlungen finden Sie immer im Datenblatt des Kabels.
5. Wie kontrolliere ich meine Schweißpfütze am besten?
Bei allen Positionen ist es am besten, den Schweißdraht auf die Vorderkante der Schweißpfütze zu richten. Wenn Sie außerhalb der Position schweißen (vertikal, horizontal oder über Kopf), bietet es sich an, die Schweißpfütze klein zu halten, um die beste Kontrolle zu erhalten. Verwenden Sie außerdem den kleinsten Drahtdurchmesser, der die Schweißfuge noch ausreichend ausfüllt.
Sie können den Wärmeeintrag und die Bewegungsgeschwindigkeit anhand der erzeugten Schweißraupe messen und entsprechend anpassen, um eine bessere Kontrolle und bessere Ergebnisse zu erzielen. Wenn Sie beispielsweise eine Schweißnaht erzeugen, die zu hoch und dünn ist, deutet das darauf hin, dass die Wärmeeinbringung zu gering ist und/oder Ihre Fahrgeschwindigkeit zu hoch ist. Eine flache, breite Sicke deutet auf eine zu hohe Wärmezufuhr und/oder eine zu langsame Fahrgeschwindigkeit hin. Passen Sie Ihre Parameter und Technik entsprechend an, um die ideale Schweißnaht zu erzielen, die eine leichte Krone aufweist, die das Metall um sie herum gerade berührt.
Diese Antworten auf häufig gestellte Fragen berühren nur einige der bewährten Methoden für das MIG-Schweißen. Befolgen Sie stets Ihre Schweißverfahren, um optimale Ergebnisse zu erzielen. Außerdem verfügen viele Hersteller von Schweißgeräten und -drähten über Telefonnummern für den technischen Support, an die sie sich bei Fragen wenden können. Sie können eine hervorragende Ressource für Sie sein.
Zeitpunkt der Veröffentlichung: 02.01.2023