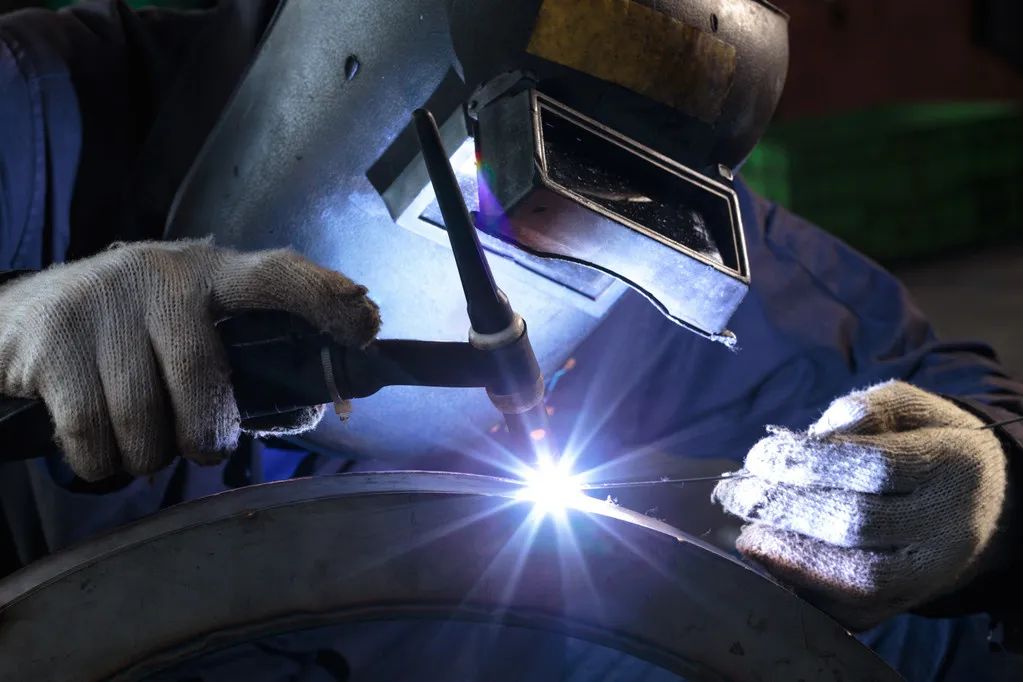
1 Übersicht
Große Containerschiffe weisen Eigenschaften wie große Länge, Containerkapazität, hohe Geschwindigkeit und große Öffnungen auf, was zu einem hohen Belastungsniveau im mittleren Bereich der Rumpfstruktur führt. Daher werden bei der Konstruktion häufig hochfeste Stahlmaterialien mit großer Dicke verwendet.
Als hocheffizientes Schweißverfahren wird häufig das Eindraht-Elektro-Gas-Vertikalschweißen (EGW) eingesetzt. Im Allgemeinen kann die maximal anwendbare Plattendicke jedoch nur 32 bis 33 mm erreichen und kann nicht für die oben genannten großen dicken Platten verwendet werden.
Die anwendbare Plattendicke des Doppeldraht-EGW-Verfahrens beträgt im Allgemeinen bis zu etwa 70 mm. Da jedoch der Schweißwärmeeintrag sehr groß ist, muss eine Stahlplatte verwendet werden, die für das Schweißen mit hohem Wärmeeintrag geeignet ist, um sicherzustellen, dass die Leistung der Schweißverbindung den Spezifikationsanforderungen entspricht.
Ohne die Verwendung von geschweißten Stahlplatten, die sich an große Wärmeeinträge anpassen können, kann daher beim vertikalen Stumpfschweißen großer und dicker Platten nur das FCAW-Mehrschichtschweißen mit mehreren Durchgängen verwendet werden, und die Schweißeffizienz ist gering.
Bei diesem Verfahren handelt es sich um ein kombiniertes FCAW+EGW-Schweißverfahren, das auf der Grundlage der oben genannten Eigenschaften entwickelt wurde und EGW nicht nur beim Schweißen großer dicker Bleche anwenden und seine hohen Effizienzvorteile voll ausnutzen kann, sondern sich auch an die Eigenschaften tatsächlicher Stahlbleche anpassen lässt . Dabei handelt es sich um ein effizientes kombiniertes Schweißverfahren, das einseitiges FCAW-Schweißen auf der Strukturoberfläche verwendet, um eine Rückseitenformung zu erreichen, und anschließend EGW-Schweißen auf der nichtstrukturellen Oberfläche durchführt.
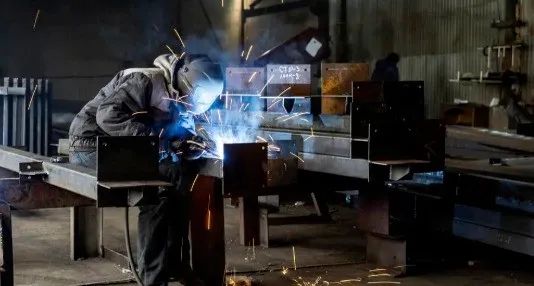
Xinfa-Schweißgeräte zeichnen sich durch hohe Qualität und niedrigen Preis aus. Weitere Informationen finden Sie unter:Schweißen und Schneiden Hersteller - China Schweißen und Schneiden Fabrik und Lieferanten (xinfatools.com)
2 Kernpunkte des kombinierten FCAW+EGW-Schweißverfahrens
(1) Anwendbare Plattendicke
34~80 mm: Das heißt, die Untergrenze ist die Obergrenze der anwendbaren Plattendicke für Monofilament-EGW; Was die Obergrenze anbelangt, so verwendet ein großes Containerschiff derzeit Stahlplatten mit großer Dicke für die Innenseite und die Deckplatten der Oberschale. Da die Dicke der Stahlplatten verschiedener Produkte unterschiedlich ist, wird sie auf 80 mm festgelegt.
(2) Dickenteilung
Das Prinzip der Aufteilung der Schweißdicke besteht darin, den hohen Effizienzvorteil des EGW-Schweißens voll auszunutzen. Gleichzeitig muss berücksichtigt werden, dass sich die Menge des beim Schweißen abgeschiedenen Metalls zwischen den beiden Methoden nicht zu stark unterscheiden darf, da es sonst schwierig wird, die Schweißverformung zu kontrollieren.
(3) Design der Verbindungsform mit kombinierter Schweißmethode
① Nutwinkel: Um zu vermeiden, dass die Nutbreite auf der FCAW-Seite zu groß wird, ist die Nut entsprechend kleiner als die normale einseitige FCAW-Schweißnut, was bedeutet, dass unterschiedliche Blechdicken unterschiedliche Fasenwinkel erfordern. Wenn die Plattendicke 30–50 mm beträgt, beträgt sie Y±5°, und wenn die Plattendicke 51–80 mm beträgt, beträgt sie Z±5°.
② Wurzelspalt: Er muss sich gleichzeitig an die Prozessanforderungen beider Schweißmethoden anpassen, d. h. G±2 mm.
③Anwendbare Dichtungsform: Herkömmliche Dreiecksdichtungen können aufgrund von Winkelproblemen die oben genannten Anforderungen an die Verbindungsform nicht erfüllen. Dieses kombinierte Schweißverfahren erfordert den Einsatz von Rundstabdichtungen. Die Durchmessergröße muss basierend auf dem tatsächlichen Montagespaltwert ausgewählt werden (siehe Abbildung 1).
(4) Grundpunkte der Schweißkonstruktion
①Schweißtraining. Die Bediener müssen eine bestimmte Schulungsdauer absolvieren. Auch Bediener mit Erfahrung im EGW-Schweißen (SG-2-Methode) von Stahlblechen normaler Dicke müssen eine Schulung absolvieren, da die Arbeitsbewegungen des Schweißdrahtes im Schmelzbad beim Schweißen dünner Bleche und großer dicker Bleche unterschiedlich sind.
②Enderkennung. Am Ende der Schweißnaht und am Lichtbogenstoppteil muss eine zerstörungsfreie Prüfung (RT oder UT) durchgeführt werden, um auf Fehler zu prüfen und die Größe der Fehler zu bestätigen. Zur Fehlerbeseitigung wird Fugenhobeln eingesetzt, zum Nacharbeitsschweißen kommen FCAW- oder SMAW-Schweißverfahren zum Einsatz.
③Bogenschließblech. Die Lichtbogen-Schließblechlänge muss mindestens 50 mm betragen. Das Lichtbogenschließblech und das Grundmaterial haben die gleiche Dicke und die gleiche Nut. ④ Während des Schweißens führt Wind zu einer Störung des Schutzgases, was zu Porenfehlern in der Schweißnaht führt, und das Eindringen von Stickstoff in die Luft führt zu einer schlechten Verbindungsleistung, sodass notwendige Windschutzmaßnahmen ergriffen werden müssen.
3 Prozessprüfung und Freigabe
(1) Testmaterialien
Die Prüfplatten und Schweißmaterialien sind in Tabelle 1 aufgeführt
(2) Schweißparameter
Die Schweißposition ist 3G und die spezifischen Schweißparameter sind in Tabelle 2 aufgeführt.
(3) Testergebnisse
Der Test wurde gemäß den LR- und CCS-Schiffsvorschriften und unter Aufsicht des Gutachters vor Ort durchgeführt. Die Ergebnisse sind wie folgt.
NDT und Ergebnisse: Die PT-Ergebnisse besagen, dass die Kanten der vorderen und hinteren Schweißnähte sauber sind, die Oberfläche glatt ist und keine Oberflächenfehler vorliegen. Die UT-Ergebnisse zeigen, dass alle Schweißnähte nach der Ultraschallprüfung qualifiziert sind (gemäß ISO 5817 Level B); Die MT-Ergebnisse zeigen, dass es sich bei den Vorder- und Rückseitenschweißnähten um magnetische Partikelfehlererkennung handelt. Nach der Inspektion gab es keine Oberflächenschweißfehler.
(4) Akzeptieren Sie die Schlussfolgerung
Nach der Durchführung von NDT- und mechanischen Eigenschaftenprüfungen an den Testschweißverbindungen entsprachen die Ergebnisse den Anforderungen der Spezifikationen der Klassifikationsgesellschaft und bestanden die Prozessgenehmigung.
(5) Effizienzvergleich
Am Beispiel einer 1 m langen Schweißnaht eines bestimmten Blechs beträgt die erforderliche Schweißzeit für das doppelseitige FCAW-Schweißen 250 Minuten; Bei Verwendung des kombinierten Schweißverfahrens beträgt die erforderliche Schweißzeit für EGW 18 Minuten, die erforderliche Schweißzeit für FCAW 125 Minuten und die Gesamtschweißzeit 143 Minuten. Das kombinierte Schweißverfahren spart fast 43 % der Schweißzeit im Vergleich zum ursprünglichen doppelseitigen FCAW-Schweißen.
4 Fazit
Das experimentell entwickelte kombinierte Schweißverfahren FCAW+EGW nutzt nicht nur die hohe Effizienz des EGW-Schweißens voll aus, sondern passt sich auch den aktuellen Eigenschaften von Stahlplatten an. Es handelt sich um eine neue Schweißprozesstechnologie mit hoher Schweißeffizienz und hoher Machbarkeit.
Als innovative Schweißverfahrenstechnologie sind deren Nutherstellung, Montagegenauigkeit, Materialauswahl, Schweißparameter usw. entscheidend und müssen bei der Umsetzung streng kontrolliert werden.
Zeitpunkt der Veröffentlichung: 22. Februar 2024