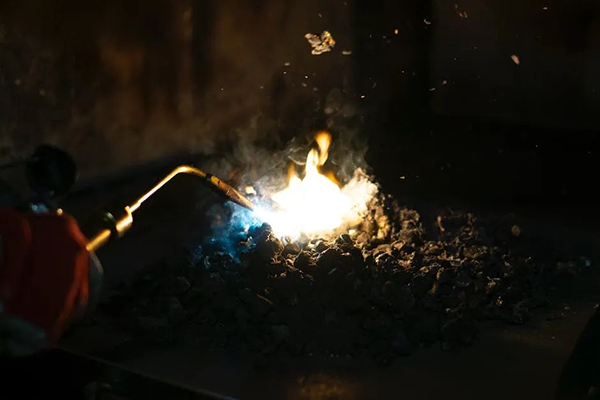
1. Hintergrundzusammenfassung
Die Anforderungen an die Pipeline-Vorfertigung in der Offshore-Technik und der petrochemischen Industrie sind relativ hoch und der Arbeitsaufwand relativ groß. Es werden die traditionelle manuelle Basis des WIG-Schweißens und das Füllen und Abdecken des MIG-Schweißens verwendet, aber die Qualität und Effizienz sind nicht ideal. In diesem Artikel wird ein neues Schweißverfahren angewendet – hocheffizientes WIG-Heißdrahtschweißen, um WIG-Basisschweißen, Füllschweißen und Deckschweißen zu erreichen, und ein hocheffizientes MIG-Schweißverfahren als Ersatz für das herkömmliche Verfahren. Durch dieses Experiment haben sich die mechanischen Eigenschaften der Forschung als wirksam erwiesen und wurden erfolgreich in der Industrie eingesetzt.
Forschungszweck
Derzeit verwendet das traditionelle Schweißverfahren manuelles WIG-Schweißen für die Basis, manuelles Schweißen oder MIG-Schweißen, Unterpulverschweißen und andere Mehrprozessmethoden zum Füllen und Abdecken, um die Schweißeffizienz zu verbessern. Diese Füll- und Abdeckmethoden lassen sich jedoch nicht einfach automatisch schweißen, sind nicht für verschiedene Rohrdurchmesser geeignet, führen relativ leicht zu Schweißfehlern und die Erfolgsquote der Schweißqualität ist durch das Betriebsniveau der Arbeiter begrenzt.
Im Vergleich zum herkömmlichen WIG-Schweißen verfügt das Heißdraht-WIG-Schweißen über eine separate Heißdraht-Stromversorgung, um den Schweißdraht auf der Basis des herkömmlichen Kaltdrahts vorzuwärmen, und erhöht die Schmelzgeschwindigkeit des Schweißdrahts, ohne die Energie der Schweißlinie zu verändern. Auf diese Weise muss der bereitgestellte Schweißlichtbogen nur eine geringe Energiemenge aufwenden, um den Schweißdraht zu schmelzen, wodurch die Effizienz der Schweißproduktion verbessert wird.
Hocheffizientes WIG-Heißdrahtschweißen ist mehr als fünfmal effizienter als herkömmliches WIG, vergleichbar mit der MIG-Schweißgeschwindigkeit, und die Abschmelzleistung wird von 0,3 bis 0,5 kg/h auf 2 bis 4 kg/h erhöht. Die heimische Heißdraht-WIG-Technologie stagniert und ist weit davon entfernt, effizientes und qualitativ hochwertiges Schweißen zu ermöglichen. Die Effizienz des ausländischen Heißdraht-WIG-Schweißverfahrens wurde nicht wesentlich verbessert und kann die Effizienz des MIG-Schweißens nicht erreichen. Daher ist es besonders dringend und wichtig, ein effizientes Heißdraht-WIG-Schweißverfahren zu entwickeln.
3.1 Experimentelle Materialien
Das Ausgangsmaterial des Versuchsrohrs ist Q235-A-Stahl mit einer Dicke von 12 mm und einem Außendurchmesser von 108 mm. Die chemische Zusammensetzung ist in Tabelle 1 aufgeführt. Die Zugfestigkeit von Q235-A-Stahl beträgt σb=482 MPa, die Streckgrenze beträgt σs=235 MPa und die Dehnung beträgt δ=26 %. Zum Einsatz kommt der Schweißdraht H08Mn2Si mit einem Durchmesser von 1,2mm. Die chemische Zusammensetzung ist in Tabelle 1 aufgeführt. Die Zugfestigkeit von H08Mn2Si-Schweißdraht beträgt σb≥500 MPa, die Streckgrenze beträgt σs≥420 MPa und die Dehnung beträgt δ≥22 %.
Xinfa-Schweißgeräte zeichnen sich durch hohe Qualität und niedrigen Preis aus. Weitere Informationen finden Sie unter:Schweißen und Schneiden Hersteller - China Schweißen und Schneiden Fabrik und Lieferanten (xinfatools.com)
3.2 Experimentelle Methode
Für den Test wurden das hocheffiziente WIG-Heißdraht-Schweißsystem KB370 mit offener Rohrschelle zur Rohrvorfertigung (siehe Abbildung 1), die Multifunktions-Schweißstromquelle PHOENIX-521 und die Heißdraht-Stromquelle Sharp Arc-200 verwendet. Es wurde das Heißdraht-WIG-Schweißverfahren verwendet. Das schematische Diagramm der Verbindung ist in Abbildung 2 dargestellt.
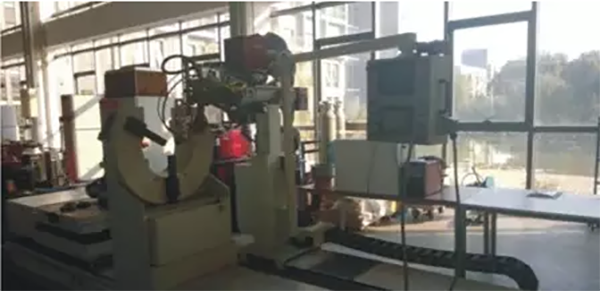
Abbildung 1 Hocheffizientes Heißdrahtschweißsystem vom Typ KB370 mit Rohrklemme
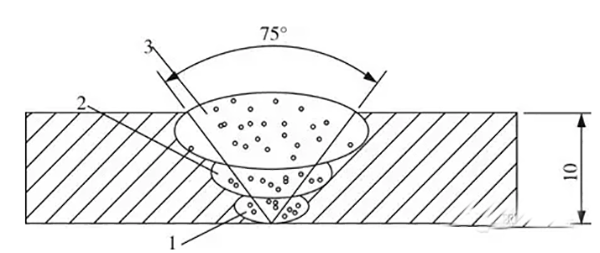
Abbildung 2 Schematische Darstellung der Verbindung
Vor dem Schweißen werden die Innen- und Außenseite der Nut des Rohrprüfstücks geschliffen und im Bereich von etwa 25 mm entrostet. Vor dem Probeschweißen wird der Rohrprüfling durch Punktschweißen fixiert. Dreipunktschweißen ist ausreichend. Die Fehlausrichtung wird innerhalb von 1,5 mm kontrolliert und es entsteht kein Spalt.
3.3 Experimentelle Ergebnisse
Nachdem die Rohrproben geschweißt waren, wurden sie zunächst einer Röntgenfehlerprüfung unterzogen und alle bestanden die I-Stufe. Andere Experimente verwendeten makroskopische metallografische, mikroskopische metallografische und mechanische Eigenschaftstests, wie in den Abbildungen 3, 4, 5, 6 bzw. Tabelle 3 dargestellt. Die Abbildungen 3 und 4 zeigen deutlich die dreischichtige Schweißnahtmorphologie, die Veränderungen in der Organisationsstruktur, die kleine Wärmeeinflusszone der Schweißnaht und keine Poren oder Risse. Tabelle 3 zeigt, dass alle Schweißnähte im Bereich des Grundmaterials gebrochen waren und die positive Biegung und die Rückbiegung den Anforderungen der Norm GB/T14452-93 entsprachen. Wie aus Tabelle 4 ersichtlich ist, werden folgende Schlussfolgerungen gezogen:
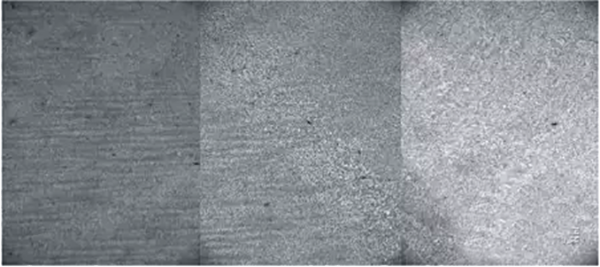
Abbildung 3 Mikrostruktur des Grundmetalls, Wärmeeinflusszone und Schweißnahtquerschnitt
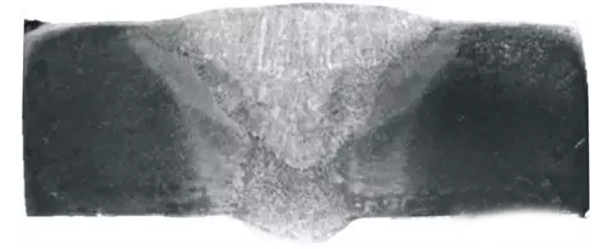
Abbildung 4 Makroskopische metallografische Struktur des Schweißnahtquerschnitts

Abbildung 5 Zugversuch
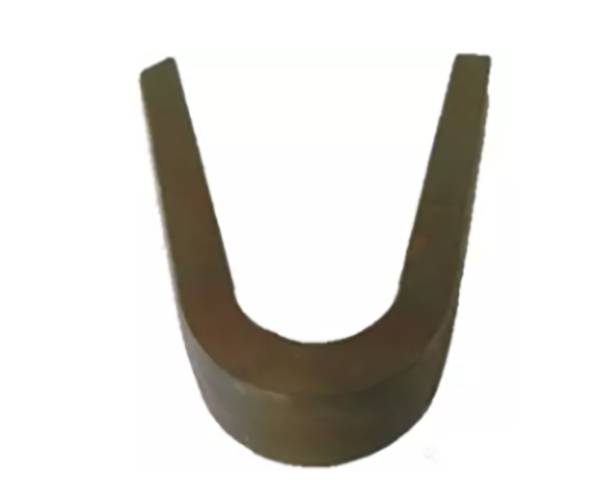
(a) Positive Biegung
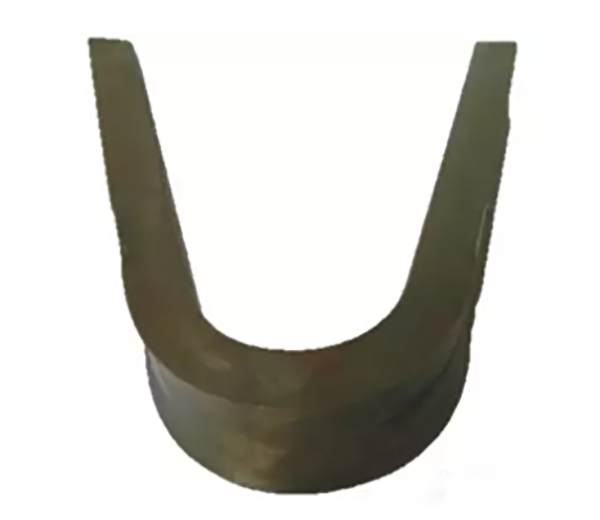
(b)Rückbeugen
Mit hocheffizientem WIG-Heißdraht können WIG-Schweißqualität und MAG-Schweißgeschwindigkeit erreicht werden, MAG-Schweißen hat jedoch Nachteile wie große Spritzer, starken Lichtbogen, große Porosität, große Linienenergie und große Schleifmenge. Obwohl die Abscheidungseffizienz hoch ist, ist sie bei hohen Qualitätsanforderungen offensichtlich nicht so stabil und zuverlässig wie das WIG-Schweißen. Die umfassende Effizienz des hocheffizienten WIG-Heißdrahtschweißens entspricht dem MAG-Schweißen oder ist geringfügig höher.
Hocheffizientes WIG-Heißdrahtschweißen und herkömmliches WIG-Kaltdrahtschweißen erzielen insgesamt eine 5- bis 10-fache Effizienzsteigerung.
4. Experimentelle Schlussfolgerung
4.1 Beim WIG-Heißdrahtschweißen kann eine Schweißnaht mit fehlerfreier Oberfläche und guter Formation erzielt werden.
4.2 Die Drahtvorschubgeschwindigkeit beim Heißdraht-WIG-Schweißen erreicht 5 m/min, bis zu 6,5 m/min, und die Schmelzrate kann 3,5 kg/h erreichen, was die Produktionseffizienz erheblich verbessert;
4.3 Der Zugbruch bei Heißdraht-WIG-Schweißungen tritt im Grundmaterial auf, was die Verbindungsleistung verbessert;
4.4 Hocheffizientes WIG-Heißdrahtschweißen erreicht tatsächlich die Schweißqualität des WIG-Schweißens und die Schweißgeschwindigkeit des MIG-Schweißens.
5. Vermarkten Sie ausgereifte Anwendungen und Aussichten
Nach fast zwei Jahren der Marktförderung und -anwendung sind wir derzeit in den Bereichen Schiffstechnik, Gas, Instrumentierung, Petrochemie und Container weit verbreitet.
Das hocheffiziente Heißdraht-WIG-Schweißverfahren eignet sich nicht nur für Kohlenstoffstahl, sondern auch für legierten Stahl, Edelstahl, Duplexstahl, Nickelbasislegierungen und andere Materialien (Experimente an verschiedenen Materialien haben gezeigt, dass dies insbesondere bei Duplexstahl der Fall ist). Beim Schweißverfahren in der Schiffstechnik und anderen Branchen bietet das hocheffiziente WIG-Heißdrahtschweißen unvergleichliche Vorteile. Es hat das Monopol des ausländischen Heißdraht-WIG-Schweißens in China gebrochen und seine Effizienz ist im Vergleich zu ausländischen Marken 1,5 bis 2-mal höher als die ausländischer Heißdrähte.
Diese Technologie schließt die Lücke im Pipeline-Vorfertigungsschweißen, ist ein innovatives Prozesstechnologieprodukt, das für die nationalen Bedingungen Chinas geeignet ist, und stellt eine bahnbrechende Innovation in der Pipeline-Vorfertigungsbranche dar. Es kann den bestehenden traditionellen Prozess der WIG-Grundierung + MAG-Füllung und -Abdeckung des Doppelverbundprozesses vollständig ersetzen, sodass Benutzer nicht wiederholt Geräte kaufen müssen, und ist ein wirklich multifunktionales und vielseitiges Rohr-Vorfertigungsschweißsystem. Das Schweißsystem mit dieser Technologie als Kernprozess wird derzeit auch auf das intelligente Pipeline-Vorfertigungssystem angewendet, und die Marktaussichten sind breit.
Zeitpunkt der Veröffentlichung: 27. August 2024