In vielen Fällen können MIG-Brenner-Verbrauchsmaterialien ein nachträglicher Einfall in den Schweißprozess sein, da Bedenken hinsichtlich Ausrüstung, Arbeitsablauf, Teiledesign und mehr die Aufmerksamkeit von Schweißern, Vorgesetzten und anderen am Betrieb beteiligten Personen dominieren. Dennoch können diese Komponenten – insbesondere Stromdüsen – einen erheblichen Einfluss auf die Schweißleistung haben.
Bei einem MIG-Schweißprozess ist die Kontaktspitze dafür verantwortlich, den Schweißstrom auf den Draht zu übertragen, während dieser durch die Bohrung verläuft, wodurch der Lichtbogen entsteht. Optimalerweise sollte der Draht mit minimalem Widerstand hindurchgeführt werden und dennoch der elektrische Kontakt bestehen bleiben. Ebenso wichtig ist die Position der Kontaktspitze innerhalb der Düse, die sogenannte Kontaktspitzenaussparung. Sie kann Qualität, Produktivität und Kosten im Schweißbetrieb beeinflussen. Dies kann sich auch auf die Zeit auswirken, die für nicht wertschöpfende Tätigkeiten aufgewendet wird, wie etwa das Schleifen oder Strahlen von Teilen, die nicht zum Gesamtdurchsatz oder zur Rentabilität des Betriebs beitragen.
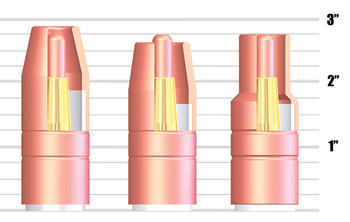
Die richtige Kontaktspitzenaussparung variiert je nach Anwendung. Da ein geringerer Drahtüberstand in der Regel zu einem stabileren Lichtbogen und einer besseren Niederspannungsdurchdringung führt, ist die beste Drahtüberstandslänge im Allgemeinen die kürzeste, die für die Anwendung zulässig ist.
Die Auswirkungen auf die Schweißqualität
Die Aussparung der Kontaktspitze beeinflusst eine Reihe von Faktoren, die wiederum die Schweißqualität beeinflussen können. Beispielsweise variiert der Stickout oder die Elektrodenverlängerung (die Länge des Drahtes zwischen dem Ende der Kontaktspitze und der Arbeitsfläche) je nach Aussparung der Kontaktspitze – konkret gilt: Je größer die Aussparung der Kontaktspitze, desto länger ist der Drahtüberstand. Mit zunehmendem Kabelüberstand steigt die Spannung und die Stromstärke nimmt ab. Wenn dies geschieht, kann sich der Lichtbogen destabilisieren, was übermäßige Spritzer, Lichtbogenwanderung, schlechte Wärmekontrolle bei dünnen Metallen und langsamere Bewegungsgeschwindigkeiten zur Folge hat.
Die Aussparung der Kontaktspitze beeinflusst auch die Strahlungswärme des Schweißlichtbogens. Wärmestau führt zu einem Anstieg des elektrischen Widerstands in den Front-End-Verbrauchsmaterialien, was die Fähigkeit der Kontaktspitze verringert, den Strom an den Draht weiterzuleiten. Diese schlechte Leitfähigkeit kann zu unzureichender Eindringung, Spritzern und anderen Problemen führen, die zu einer inakzeptablen Schweißnaht oder zu Nacharbeiten führen können.
Außerdem verringert zu viel Hitze im Allgemeinen die Lebensdauer der Kontaktspitze. Das Ergebnis sind höhere Gesamtkosten für Verbrauchsmaterialien und größere Ausfallzeiten beim Austausch der Kontaktdüsen. Da bei einem Schweißvorgang fast immer der Arbeitsaufwand die größten Kosten darstellt, können sich diese Ausfallzeiten zu unnötigen Erhöhungen der Produktionskosten summieren.
Ein weiterer wichtiger Faktor, der durch die Aussparung der Kontaktspitze beeinflusst wird, ist die Schutzgasabdeckung. Wenn die Düse durch die Aussparung der Kontaktspitze weiter vom Lichtbogen und der Schweißpfütze entfernt ist, ist der Schweißbereich anfälliger für Luftströme, die das Schutzgas stören oder verdrängen können. Eine schlechte Schutzgasabdeckung führt zu Porosität, Spritzern und unzureichender Penetration.
Aus all diesen Gründen ist es wichtig, die richtige Kontaktaussparung für die Anwendung zu verwenden. Es folgen einige Empfehlungen.
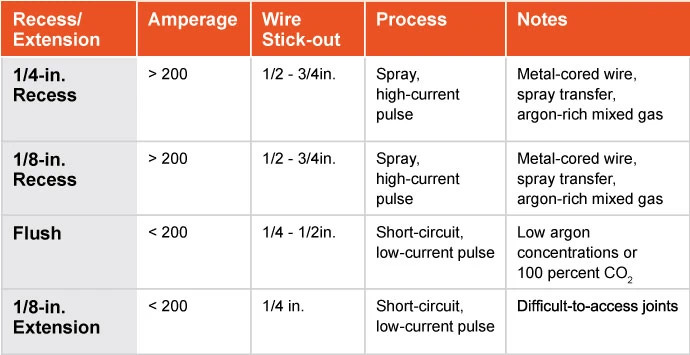
Abbildung 1: Die richtige Kontaktspitzenaussparung variiert je nach Anwendung. Konsultieren Sie immer die Empfehlungen des Herstellers, um die richtige Aussparung für die Kontaktspitze für die jeweilige Aufgabe zu bestimmen.
Arten von Kontaktspitzenaussparungen
Der Diffusor, die Spitze und die Düse sind die drei Hauptbestandteile der MIG-Brenner-Verbrauchsmaterialien. Der Diffusor wird direkt am Pistolenhals befestigt, leitet Strom zur Kontaktspitze und leitet das Gas in die Düse. Die Spitze verbindet sich mit dem Diffusor und überträgt den Strom auf den Draht, während dieser ihn durch die Düse und zum Schweißbad führt. Die Düse wird am Diffusor befestigt und dient dazu, das Schutzgas auf den Schweißlichtbogen und die Schweißpfütze zu fokussieren. Jede Komponente spielt eine entscheidende Rolle für die Gesamtqualität der Schweißnaht.
Für MIG-Brenner-Verschleißteile stehen zwei Arten von Kontaktspitzenaussparungen zur Verfügung: fest oder einstellbar. Da eine einstellbare Kontaktspitzenaussparung auf unterschiedliche Tiefen- und Erweiterungsbereiche geändert werden kann, haben sie den Vorteil, dass sie den Aussparungsanforderungen verschiedener Anwendungen und Prozesse gerecht werden können. Sie erhöhen jedoch auch das Risiko menschlicher Fehler, da Schweißer sie durch Manövrieren der Position der Düse oder über einen Verriegelungsmechanismus, der die Kontaktspitze in einer bestimmten Aussparung sichert, einstellen.
Um Abweichungen zu vermeiden, bevorzugen einige Unternehmen Spitzen mit fester Aussparung, um eine gleichmäßige Schweißnaht zu gewährleisten und von einem Schweißer zum nächsten gleichbleibende Ergebnisse zu erzielen. Bei automatisierten Schweißanwendungen, bei denen eine konsistente Spitzenposition von entscheidender Bedeutung ist, sind Spitzen mit fester Aussparung üblich.
Verschiedene Hersteller stellen Verbrauchsmaterialien für unterschiedliche Kontaktspitzen-Aussparungstiefen her, die typischerweise von einer 1⁄4-Zoll-Aussparung bis zu einer 1⁄8-Zoll-Verlängerung reichen.
Bestimmung der richtigen Aussparung
Die richtige Kontaktspitzenaussparung variiert je nach Anwendung. Eine gute Regel, die Sie berücksichtigen sollten, ist, dass unter den meisten Bedingungen mit zunehmendem Strom auch die Pause zunehmen sollte. Da ein geringerer Drahtüberstand in der Regel zu einem stabileren Lichtbogen und einer besseren Niederspannungsdurchdringung führt, ist die beste Drahtüberstandslänge im Allgemeinen die kürzeste, die für die Anwendung zulässig ist. Nachfolgend finden Sie einige Richtlinien. Weitere Hinweise finden Sie auch in Abbildung 1.
1. Für Impulsschweißen, Sprühübertragungsprozesse und andere Anwendungen mit mehr als 200 Ampere wird eine Kontaktspitzenvertiefung von 1/8 Zoll oder 1/4 Zoll empfohlen.
2. Bei Anwendungen mit höheren Strömen, wie z. B. beim Verbinden dicker Metalle mit Drähten mit großem Durchmesser oder Metallkerndrähten im Sprühübertragungsverfahren, kann eine versenkte Kontaktspitze auch dazu beitragen, die Kontaktspitze von der hohen Hitze des Lichtbogens fernzuhalten. Die Verwendung eines längeren Drahtüberstands für diese Prozesse trägt dazu bei, das Auftreten von Rückbrand (wo der Draht schmilzt und sich an der Kontaktspitze festsetzt) und Spritzer zu reduzieren, was dazu beiträgt, die Lebensdauer der Kontaktspitze zu verlängern und die Kosten für Verbrauchsmaterialien zu senken.
3.Bei Verwendung eines Kurzschlussübertragungsverfahrens oder eines Niedrigstrom-Impulsschweißens wird im Allgemeinen eine bündige Kontaktspitze mit einem Drahtüberstand von etwa 1⁄4 Zoll empfohlen. Die relativ kurze Stickout-Länge ermöglicht die Kurzschlussübertragung zum Schweißen dünner Materialien ohne Gefahr eines Durchbrennens oder Verziehens und mit geringer Spritzerbildung.
4.Verlängerte Kontaktspitzen sind normalerweise einer sehr begrenzten Anzahl von Kurzschlussanwendungen mit schwer zugänglichen Verbindungskonfigurationen vorbehalten, wie z. B. tiefen und schmalen V-Nut-Verbindungen beim Rohrschweißen.
Diese Überlegungen können bei der Auswahl hilfreich sein, aber ziehen Sie immer die Empfehlungen des Herstellers zu Rate, um die richtige Kontaktspitzenaussparung für die jeweilige Aufgabe zu ermitteln. Denken Sie daran, dass die richtige Position das Risiko übermäßiger Spritzer, Porosität, unzureichender Eindringung, Durchbrennen oder Verziehen bei dünneren Materialien und mehr verringern kann. Wenn ein Unternehmen außerdem erkennt, dass die Kontaktspitzenvertiefung die Ursache für solche Probleme ist, kann dies dazu beitragen, zeitraubende und kostspielige Fehlerbehebungsmaßnahmen oder Nacharbeiten wie Nacharbeiten zu vermeiden.
Zusätzliche Informationen: Wählen Sie hochwertige Tipps
Da Kontaktdüsen ein wichtiger Faktor für die Herstellung hochwertiger Schweißnähte und die Reduzierung von Ausfallzeiten sind, ist es wichtig, eine qualitativ hochwertige Kontaktdüse auszuwählen. Obwohl diese Produkte möglicherweise etwas mehr kosten als minderwertige Produkte, bieten sie einen langfristigen Wert, indem sie die Lebensdauer verlängern und die Ausfallzeiten für die Umstellung reduzieren. Darüber hinaus können höherwertige Kontaktspitzen aus verbesserten Kupferlegierungen hergestellt werden und werden in der Regel mit engeren mechanischen Toleranzen bearbeitet, wodurch eine bessere thermische und elektrische Verbindung entsteht und die Wärmeentwicklung und der elektrische Widerstand minimiert werden. Hochwertigere Verbrauchsmaterialien verfügen in der Regel über eine glattere Mittelbohrung, was zu weniger Reibung beim Durchführen des Drahtes führt. Das bedeutet eine gleichmäßige Drahtförderung mit weniger Widerstand und weniger potenziellen Qualitätsproblemen. Kontaktspitzen höherer Qualität können auch dazu beitragen, Rückschläge zu minimieren und einen unregelmäßigen Lichtbogen zu verhindern, der durch inkonsistente elektrische Leitfähigkeit verursacht wird.
Zeitpunkt der Veröffentlichung: 01.01.2023